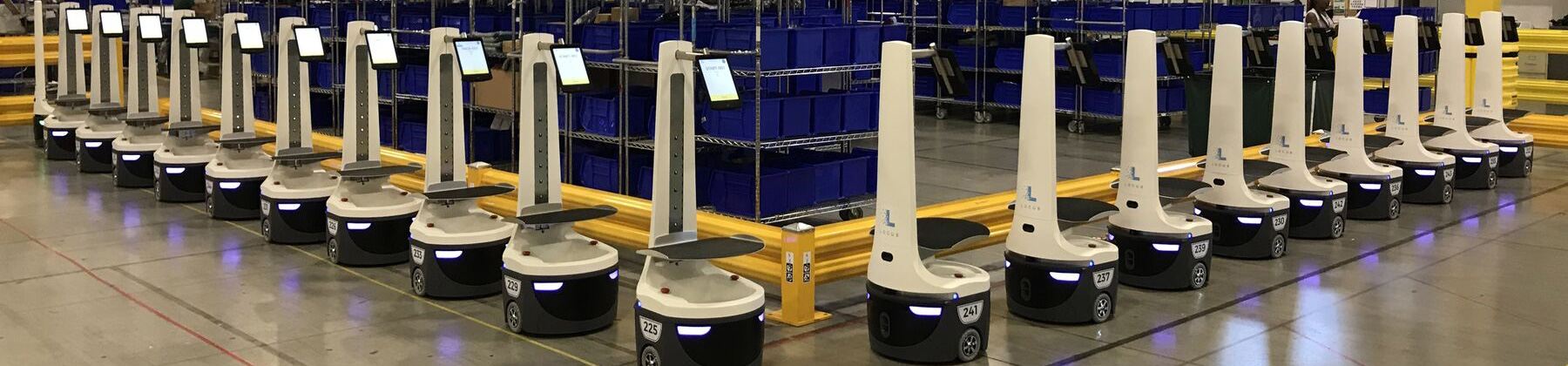
Automation aims to improve efficiency. When done well, automated sites are more productive, run more smoothly, have faster processing times, improve worker safety and are more efficient from a total cost standpoint (operating and capital expenses). Key logistics operations typically comprise the following:
-
Unloading/receiving.
-
Put-away.
-
Storage.
-
Picking.
-
Packing.
-
Loading/shipping.
All logistics operations must assess their requirements and capabilities across these functions and invest accordingly. For quite some time, the logistics industry has leveraged a wide range of productivity-enhancing equipment to accomplish these functions, such as racks and forklifts.
To define and segment automation technologies from other types of equipment, the key differentiator is autonomy from human control. Here again, some of these productivity-enhancing technologies, including complex conveyance systems, pneumatic rollers and automated guided vehicles, are not new to logistics operations.
Automation technologies can be grouped into two categories:
Fixed automation. These types of automation tend to be large, bespoke or semi-bespoke, fixed capacity with limited flexibility, and high-priced installations. Common types include:
-
Conveyor belts.
-
Automatic sorters.
-
Palletizers.
-
Pallet shuttles.
-
Automated Storage and Retrieval Systems (AS/RS).
Mobile and semi-mobile automation. These types of automation tend to be discrete robotics solutions that work in a range of environments and offer greater flexibility for scaling up/down as needed. Common types include:
-
Automated Guided Vehicles (AGV) such as autonomous forklifts.
-
Autonomous Mobile Robots (AMR) such as some co-bots.
-
Specialized/niche automation such as automated boxing and
trailer unloaders.
No one solution exists. Many automation solutions aim to address one or two of the six core warehouse functions. Each step engenders substantially different actions, movements, variability and levels of complexity; further, each requires specialized equipment. Integrations between core functions and across automation technologies are especially complex and expensive. For example, pneumatic rollers will accomplish only put-away and picking with dedicated lanes for each. Mobile technologies and co-bots aim at the simplest functions to automate, offering the fastest ROIs and easier integrations while allowing users to build on human talent at the core of operations.
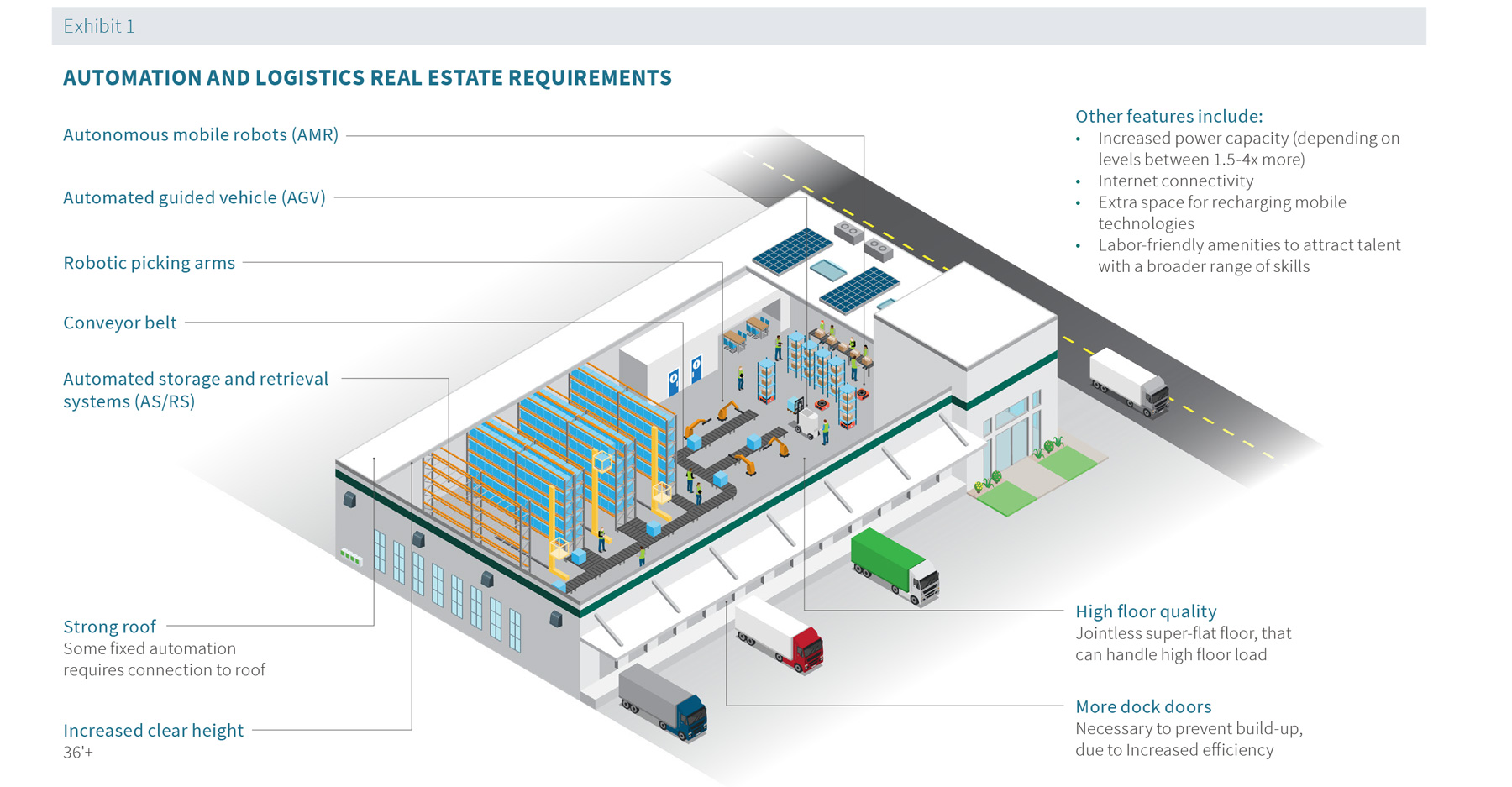